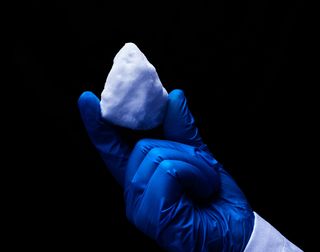
Reliable & Deployable
Molten Salt Reactors
(MSRs)
Molten salt-cooled, liquid-fueled reactors make nuclear power safer, cheaper, and more accessible than ever.
Molten Salt Cooling
Cooling with molten salt instead of water allows us to operate at the pressure of household pipes. We can also operate at significantly higher temperatures than conventional reactors, creating an opportunity to serve industries that require 24/7 sources of power and high heat. MSRs also open the door to recycling spent nuclear fuel.
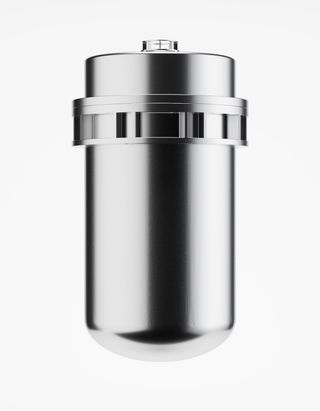
Salt Cooled
Improved Efficiency
Industrial Heat Applications
No phase transition to steam
Enhanced Safety
Liquid Fueled
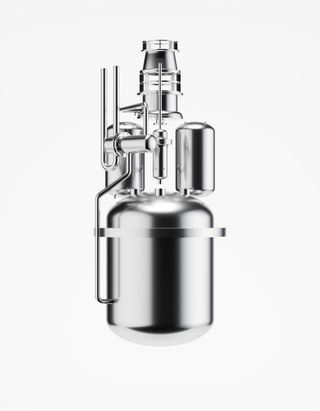
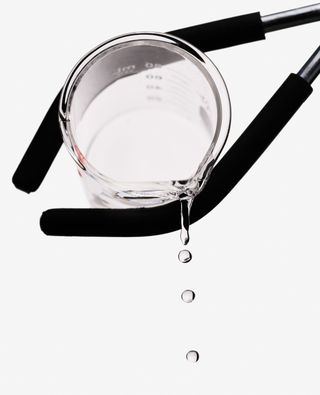
Process
A Liquid-Fueled Molten Salt Reactor (LF-MSR) is a type of advanced reactor that uses liquid fuel in the form of molten salts for both the fuel and the coolant. The most commonly discussed molten salt for this application is a mixture of lithium fluoride (LiF) and beryllium fluoride (BeF2) salts, and/or thorium fluoride salts. LF-MSRs operate at high temperatures and have unique features that differentiate them from traditional solid-fuel reactors.
Liquid Fuel
In liquid-fuel MSR designs, the fission products dissolve in the fuel salt and are ideally removed continuously in an adjacent online reprocessing loop and replaced with fissile uranium, plutonium and other actinides or, potentially, fertile Th-232 or U-238.
Liquid fuel eliminates the possibility of a meltdown making MSRs “walk away safe.” If a malfunction occurs, the fuel salt cools, turns into a solid, and is safely contained within the system. They are also far more efficient, targeting greater than 90% burnup of the fuel as opposed to the less than 5% consumption rate of current solid fuel reactors.
Modular
Production +
Assembly
We are developing factory-built modular molten salt reactors that are sized to be shipped via truck or rail anywhere in the world. Reactors can be deployed in a variety of configurations to meet the needs of industries such as data centers, water desalination plants and grid-level power.
Our reactors are ready to meet the demand for 24/7, carbon-free energy.
Reactor Core and Fuel
Natura Resources MSRs are liquid-fueled meaning fissile UF4 material is dissolved in a molten salt mixture. As this molten fuel salt moves through the reactor core, a fission reaction takes place producing tremendous quantities of energy and temperatures over 600°C.
Walk-Away Safe Shutdown
To shut down the reactor the fuel salt is drained into a drain tank located directly below the reactor core. The geometry of the drain tank and lack of moderator ensure that the fission process ceases. Once in the drain tank the fuel salt can be externally heated to remain in liquid form, or it can be allowed to cool and return to a solid state once temperatures drop below 450°C.
Isotope Production
When a Uranium atom fissions it splits into two or more large fragments known as fission products. Many of these fission products such as Molybdenum-99 are vital isotopes for medical diagnostics and treatment. These fission products in solid-fueled reactors are contained within the fuel rods or pellets making them inaccessible. With the fuel dissolved in a molten salt these fission products are found in both the liquid and gas phases and can be extracted via a variety of methods.
Heat Transfer
The primary heat removal system transfers the heat generated in the fission process through a cooling loop and to a separate process fluid that can be then used for a wide variety of end use applications.
End Uses
MSRs are flexible in their potential end use applications. The secondary heat removal system will provide a heat transfer fluid with temperatures exceeding 600°C that can be utilized for a variety of applications, including, but not limited to: electricity generation, high process heat applications such as hydrogen or steel production and water desalination. The exact specifications for the secondary coolant system and the corresponding balance of plant are highly dependent on the end use applications and designed to meet customer requirements.